Mastering Industry Safety: Best Practices in the Construction Sector
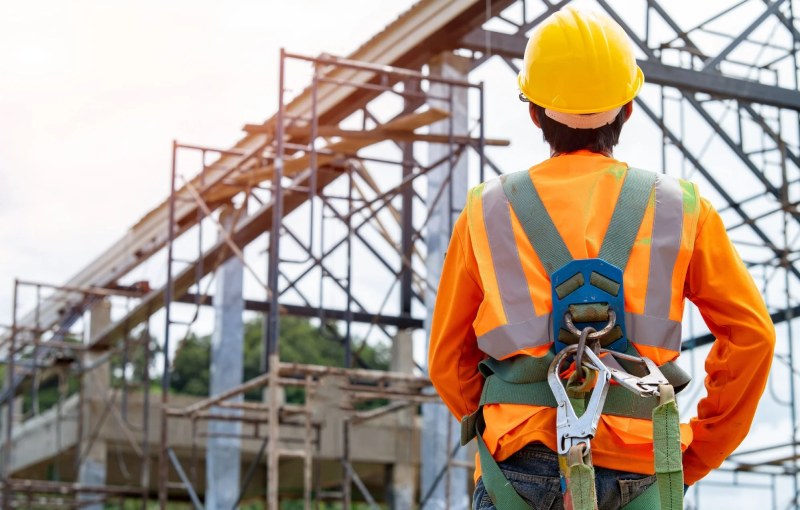
Pressure on the construction sector is at an all-time high.
It’s estimated that the industry needs to attract over 500,000 more workers to meet current labor demands, with career changes and retirement partially to blame for ongoing staff shortages.
While there’s no one-size-fits-all solution to the challenges in construction across the US, it’s certain that staff retention should be a priority. And when it comes to practical solutions to this challenge, enhanced staff safety makes a solid foundation.
In this article, we’ve covered the most critical ways to ensure best practice in relation to keeping safe and compliant in the construction industry.
Health and safety in construction: Four ways to ensure best practice
- Risk Assessment
Identifying potential hazards is an imperative process on any construction site.
Common hazards including falls, electrocution, and struck-by incidents should always be prioritized, but you’ll need to think about all areas – even the niche ones. In colder states like Minnesota or Montana, all construction groups should guarantee winter weather preparedness.
Your senior leadership team, plus stakeholders wherever appropriate, need to discuss the strategies used for mitigating risks. These might include working through engineering controls, administrative measures, and personal protective equipment, as we explain in our next point.
- Personal Protective Equipment
The importance of wearing appropriate PPE onsite should never be underestimated.
From power tools to ramps and heavy apparatus and corrosive chemicals, the risks in construction are wide-ranging and far-reaching. There are therefore various types of PPE required for different tasks in the workplace.
Core PPE in construction should be high quality and approved by the relevant trade bodies for industry use. It should also be issued directly by the employer to the teams using it, professionally maintained, and replaced whenever necessary or appropriate.
Specific items might include hard hats, safety glasses, gloves, and protective footwear. To ensure proper PPE fit in construction, it’s worth consulting expert guidance on selection and maintenance.
- Safe Working Practices
Each construction firm should know and implement specific procedures for safely performing common construction tasks. These might include excavation, scaffolding, welding, and heavy equipment operation. However, implementing regular risk assessments will help to identify any room for enhanced or additional strategies.
Safety protocols are detailed in the OSHA laws and regulations, applicable to all industry organizations to prevent accidents and injuries on construction sites. Electrical safety is also paramount in construction, even when it comes to smaller key components like variable transformers. Always check, maintain, and upgrade electronics where required.
- Emergency Preparedness
Lastly, in the current age, it’s more important than ever before to know how to react to an emergency. This preparedness extends to natural disasters like tornadoes and earthquakes, which are becoming increasingly common across the US.
All construction firms must develop and implement emergency action plans. In the event of fire, for example, a drill might involve full evacuation, disengaging systems, and taking an immediate register of staff present. Training drills for various situations keep a team safe and in the know.